9 Proven Techniques for Building Hardness Swade: Achieving Unmatched Durability
Building materials that are both durable and reliable is essential for any craftsperson, engineer, or builder. Building hardness swade is a term that refers to the process of strengthening materials to improve their resistance to wear, pressure, and time. Whether you are constructing large buildings, creating intricate designs, or developing tools, understanding how to build hardness is key to ensuring the longevity and functionality of your projects.
In this blog post, we will explore 9 proven techniques for building hardness swade that can be applied to various materials, from metals to wood and composites. Each technique is essential for mastering the art of creating durable, long-lasting structures and products. Let’s dive in and uncover these strategies!
1. Understanding Building Hardness Swade: What It Is and Why It Matters
Before jumping into the techniques, it’s crucial to understand what building hardness swade entails. Hardness refers to a material’s ability to withstand deformation, indentation, and wear, which is essential in ensuring that products and structures last over time. Swade, in this context, emphasizes a refined, targeted approach to shaping and strengthening materials to enhance their hardness.
Whether you are working with metals, plastics, or even wood, building hardness ensures that the material retains its form under stress, pressure, and wear. Building hardness swade is about finding the perfect balance between strength and flexibility, optimizing the material’s properties for its intended use.
2. Choosing the Right Material: Foundation of Hardness
The first step in building hardness swade is selecting the right material for your project. Different materials have different inherent hardness levels, and choosing the best one is critical for achieving the desired strength and durability.
Metals such as steel, titanium, and aluminum are often used in heavy-duty construction due to their high hardness and resilience. However, softer materials like wood, leather, and plastics can be treated and processed to achieve higher hardness as well. Understanding the properties of the materials you work with will guide you in achieving optimal results in building hardness swade.
For example, steel can be an excellent material for structural applications, but if you’re working on a delicate wooden piece of furniture, treating the wood to build hardness can result in a more durable and aesthetically pleasing outcome.
3. Heat Treatment: The Core of Building Hardness Swade
Heat treatment is one of the most effective and widely used methods in building hardness swade, especially for metals. The process involves heating the material to a specific temperature and then cooling it in a controlled environment. This process alters the material’s microstructure, resulting in increased hardness and strength.
For example, in steel, heat treatment such as quenching (rapid cooling) or annealing (controlled cooling) can create a material that resists wear, corrosion, and stress. The key to successful heat treatment is understanding the optimal temperature ranges for different materials and knowing how to manipulate cooling rates for specific outcomes.
This technique allows builders and manufacturers to create materials that are both durable and capable of withstanding harsh conditions, making it a vital component of building hardness swade.
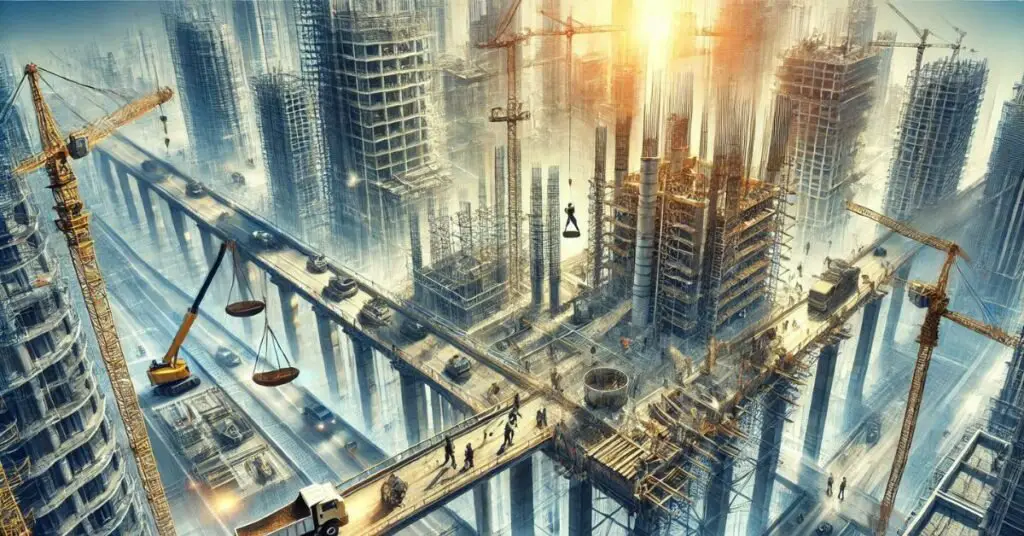
4. Surface Hardening: Strengthening the Outer Layers
Surface hardening techniques are commonly used in building hardness swade to improve the durability of the material without affecting its core properties. Surface hardening focuses on hardening the outer layer of a material while keeping the inside relatively softer and more flexible.
Methods like induction hardening, nitriding, and case hardening are ideal for increasing surface hardness in metals. These processes work by applying heat to the surface, then cooling it rapidly, forming a hardened exterior layer that resists wear and impact. This technique is commonly used in automotive parts, gears, and tools where the external surface is subject to high levels of friction.
Surface hardening is an effective technique for improving durability without compromising the material’s overall functionality and integrity, making it a valuable part of the building hardness swade process.
5. Tempering: Reducing Brittleness for Optimal Hardness
Tempering is a crucial process that follows heat treatment in building hardness swade. After materials like steel undergo heat treatment to increase their hardness, they often become too brittle. Tempering helps reduce this brittleness while maintaining the hardness achieved through heat treatment.
The tempering process involves reheating the hardened material to a lower temperature and allowing it to cool slowly. This relieves internal stresses, reduces brittleness, and improves toughness. The final result is a material that combines both strength and resilience, perfect for use in applications where flexibility is just as important as hardness.
For example, tempered steel is commonly used in tools, knives, and machinery parts because of its improved toughness and resistance to cracking. This makes tempering a key step in ensuring long-term durability in building hardness swade.
6. Laser Hardening: Precision at Its Best
Laser hardening is a modern technique used in building hardness swade to enhance the hardness of a material with great precision. This process involves using a high-powered laser to selectively heat and harden the surface of materials.
Laser hardening offers several advantages, including the ability to target specific areas of the material that require enhanced strength while leaving other areas unaffected. It is especially useful for parts with complex geometries or intricate designs where conventional heat treatment methods might not be effective.
This technique provides excellent control over the hardness process and can be applied to a wide range of materials, including metals, polymers, and composites, making it an advanced and valuable addition to the toolbox of anyone practicing building hardness swade.
7. Plasma Nitriding: Enhanced Hardness and Corrosion Resistance
Plasma nitriding is another advanced method that enhances the surface hardness of metals and alloys. This process involves introducing nitrogen into the material’s surface in a controlled environment, using plasma to accelerate the process. The result is a hard, durable surface layer that also offers excellent corrosion resistance.
Plasma nitriding is particularly effective for materials that require a high degree of wear resistance, such as components used in the automotive and aerospace industries. This process also enhances fatigue strength and surface toughness, making it a vital technique for building hard Swade in high-performance materials.
8. Cold Working: Hardening Through Deformation
Cold working, also known as cold working hardening, involves physically deforming a material at room temperature to increase its hardness. This process works by introducing dislocations into the material’s structure, making it harder and stronger.
Common methods of cold working include rolling, drawing, and bending. For example, cold-drawn steel is often stronger and harder than hot-rolled steel due to the deformation process. Cold working is a valuable technique for achieving enhanced hardness in metals and alloys used in structural applications, tools, and machinery.
By applying cold working techniques, builders and manufacturers can achieve high-strength materials without the need for additional heat treatments or complicated processes.
9. Protective Coatings: Preserving Hardness Over Time
Lastly, protective coatings play a crucial role in maintaining the hardness and durability of materials. Even after achieving the desired hardness, materials can degrade due to external factors such as moisture, chemicals, and environmental stress.
Applying protective coatings such as paints, varnishes, or specialized chemical treatments can help preserve the hardness and integrity of the material over time. For example, coating steel parts with a corrosion-resistant finish can prevent rust and extend the lifespan of the material, ensuring that the hardness remains intact.
Protective coatings are an essential final step in building hardness swade, ensuring that materials remain durable and resistant to environmental factors long after they are created.
Conclusion: Perfecting the Art of Building Hardness Swade
Mastering building hardness swade is an essential skill for anyone working with materials that need to withstand wear and stress. By applying the techniques we’ve discussed—ranging from traditional heat treatment to modern technologies like laser hardening and plasma nitriding—you can create materials that offer exceptional durability and longevity.
By choosing the right materials, applying the correct treatments, and incorporating advanced technologies, you can ensure that your projects are not only strong but also built to stand the test of time. Whether you’re constructing a building, designing tools, or crafting intricate pieces, building hardness is key to success. Embrace these proven techniques, and you’ll be on your way to creating materials and structures that last for years to come.
Pingback: What is a Sellic in Hairstyling? 5 Key Facts You Need to Know - hayathomeessentials.com